Plastic extrusion for thermoplastics, PVC, and engineering plastics
Plastic extrusion for thermoplastics, PVC, and engineering plastics
Blog Article
Checking Out the Different Methods and Technologies Behind Plastic Extrusion
The world of plastic extrusion is a blend of precision, technology, and innovation, crucial to many sectors worldwide. Advanced equipment, electronic controls, and a range of products assemble in this complicated procedure, producing top notch, durable items.
Recognizing the Essentials of Plastic Extrusion
The process of plastic extrusion, often hailed as a keystone in the world of production, creates the bedrock of this conversation. In significance, plastic extrusion is a high-volume production process in which raw plastic product is thawed and created into a continuous profile. The procedure begins with feeding plastic products, usually in the type of pellets, into a heated barrel.
The Function of Various Materials in Plastic Extrusion
While plastic extrusion is a typically utilized method in manufacturing, the materials utilized in this procedure substantially influence its final outcome. Different sorts of plastics, such as pvc, polyethylene, and abs, each offer special homes throughout product. For example, polyethylene, known for its toughness and adaptability, is typically utilized in product packaging, while PVC, renowned for its strength and resistance to ecological aspects, is made use of in building and construction. ABS, on the various other hand, combines the very best features of both, leading to high-impact resistance and toughness. The choice of product not just influences the product's physical buildings however also impacts the extrusion speed and temperature level. For that reason, makers should thoroughly consider the properties of the material to optimize the extrusion procedure.
Strategies Made Use Of in the Plastic Extrusion Process
The plastic extrusion procedure involves different strategies that are crucial to its procedure and effectiveness (plastic extrusion). The conversation will certainly start with a simplified description of the essentials of plastic extrusion. This will be adhered to by a break down of the procedure in information and an expedition of techniques to boost the performance of the extrusion strategy
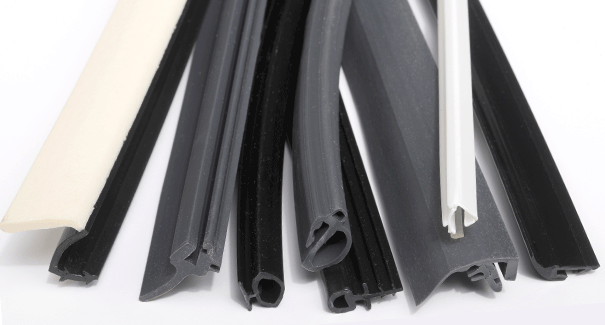
Recognizing Plastic Extrusion Fundamentals
In the world of production, plastic extrusion stands as a basic process, essential in the manufacturing of a plethora of daily products. At its core, plastic extrusion entails changing raw plastic material into a constant profiled shape. This is accomplished by thawing the plastic, typically in the type of granules or pellets, and forcing it via a shaped die. The resulting product is a long plastic item, such as a cord, panel, or pipeline finishing, that maintains the form of the die. This cost-effective method is extremely flexible, able to create intricate forms and suit a wide array of plastic products. Essential understanding of these fundamentals permits further exploration of the much more elaborate elements of plastic extrusion.
Thorough Extrusion Refine Breakdown

Improving Extrusion Strategy Efficiency
Performance gains in the plastic extrusion process can considerably influence both the high quality of the end product and the total efficiency of the operation. Continual optimization of the extrusion technique is vital to preserving an affordable edge. Methods that enhance performance often include precise control of temperature and pressure throughout the procedure. Modern innovations, such as electronic systems and sensors, have been critical in accomplishing this control. The use of top notch raw products can reduce waste and boost output quality. Routine upkeep of extrusion equipment can likewise minimize downtimes, therefore boosting efficiency. Adopting lean manufacturing concepts can assist get rid of unneeded steps in the process, advertising effectiveness gains.
Just How Modern technology Is Changing the Face of Plastic Extrusion
The arrival of new modern technology has significantly changed the landscape of plastic extrusion. It has actually caused the growth of advanced extrusion machinery, which has actually boosted the effectiveness and top quality of the plastic extrusion process. Moreover, innovations in the extrusion procedure have actually also been driven by technical improvements, providing improved abilities and versatility.
Advanced Extrusion Equipment
Changing the world of plastic extrusion, progressed equipment imbued with innovative modern technology is introducing a new age of effectiveness and accuracy. These machines, geared up with innovative features like automatic temperature control systems, make certain ideal conditions for plastic processing, thus lessening waste and enhancing product quality. High-speed extruders, for example, intensify outcome prices, while twin-screw extruders provide exceptional blending abilities, crucial for producing intricate plastic blends. In addition, computerized control systems use extraordinary accuracy in procedures, reducing human mistake. These machines are designed for long life, reducing downtime and upkeep expenses. While these developments are already amazing, the continual evolution of technology promises also better leaps onward in the area of plastic extrusion equipment.
Technologies in Extrusion Procedures
Taking advantage of the power of modern-day site web innovation, plastic extrusion processes are undergoing a transformative transformation. Developments such as digital numerical control (CNC) systems currently enable for even more precision and uniformity in the manufacturing of extruded plastic. Automation better improves effectiveness, lowering human error and labor their explanation expenses. The assimilation of expert system (AI) and maker knowing (ML) formulas is reinventing quality assurance, anticipating inconsistencies, and enhancing the total efficiency of extrusion processes. With the introduction of 3D printing, the plastic extrusion landscape is additionally broadening right into brand-new realms of possibility. These technical advancements are not only enhancing the quality of extruded plastic products yet additionally propelling the market in the direction of an extra lasting, efficient, and cutting-edge future.
Real-World Applications of Plastic Extrusion
Plastic extrusion, a functional and effective procedure, locates use in numerous real-world applications. It's predominantly utilized in the manufacturing field, where it's used to create a myriad of products such as pipelines, tubes, home window structures, weather condition removing, and fencing. The vehicle industry also utilizes this technology to produce parts like plastic and trim sheet. The clinical field depends on extrusion for the fabrication of catheters, IV tubes, and other clinical devices. Even in food manufacturing, extrusion contributes in creating products like pasta or grain. The toughness and adaptability of plastic extrusion, paired with its cost-effectiveness, make it a vital process across numerous sectors, underscoring its prevalent useful applications.
The Future of Plastic Extrusion: Forecasts and Trends
As we look to the perspective, it ends up being clear that plastic extrusion is positioned for substantial innovations and transformation. Eco-friendly choices to conventional plastic, such as bioplastics, are likewise anticipated to acquire grip. These fads show a dynamic, progressing future for plastic extrusion, driven by technological technology and a commitment to sustainability.

Conclusion
To conclude, plastic extrusion is an intricate procedure that makes use of advanced modern technology and differed products to create diverse products. Technical improvements, such as digital controls, boost the production process and guarantee constant results. Furthermore, the industry's emphasis on sustainability and intelligent equipment suggests a promising future. As plastic production remains to develop, it remains a vital part of several sectors worldwide.
In significance, plastic extrusion is a high-volume manufacturing procedure in which raw plastic product is thawed and developed into a constant account.While plastic extrusion is a typically utilized strategy in my response production, the materials utilized in this process considerably influence its final output. At its core, plastic extrusion involves changing raw plastic material into a constant profiled form. It has actually led to the advancement of sophisticated extrusion equipment, which has actually boosted the efficiency and top quality of the plastic extrusion procedure.In verdict, plastic extrusion is a complex procedure that utilizes innovative modern technology and differed products to create diverse products.
Report this page